Working with expanding foam can be challenging, but the right steps make it easier. Whether you’re insulating your home or sealing gaps, knowing how to handle the foam is key. This guide will show you how to smooth out expanding foam safely and effectively, ensuring your project looks perfect.
Key Takeaways
- Wait 12-24 hours for the foam to fully cure before attempting to trim or smooth it out.
- Use ventilation and personal protective equipment (PPE) when working with uncured foam to minimize exposure to harmful fumes.
- Select the right cutting tools based on the foam’s open-cell or closed-cell structure to avoid damaging the surface.
- Apply a thin layer of wall filler over the cured foam for a smooth painting surface.
- Proper cleanup and disposal of foam waste are essential for a safe and eco-friendly project.
Understanding Expanding Foam and Its Properties
Expanding foam, also known as polyurethane foam or spray foam, is a key construction material. It can grow up to 30-60 times its liquid size. This makes it great for insulation and sealing. Knowing the types of expanding foam and their properties is key to picking the right one for your project.
Read also: How Do You Get Dried Expanding Foam off
Types of Expanding Foam: Open-Cell vs. Closed-Cell
There are two main types of expanding foam: open-cell and closed-cell. Open-cell foam has small air bubbles that let air through. It’s flexible and good for insulation. Closed-cell foam has tight air bubbles that block air and water. It’s rigid and durable.
Common Applications and Uses
Expanding foam is used in many construction and home improvement tasks. It’s great for filling gaps around walls, pipes, windows, and doors. It seals out drafts and keeps moisture out. Its ability to insulate and manage dampness helps prevent mold and saves energy.
Read also: Is Expanding Foam Waterproof?
Safety Considerations Before Starting
Working with expanding foam requires safety first. The chemicals can irritate the nose, cause breathing problems, and skin issues. Wear personal protective equipment like gloves, long clothes, eye protection, and a mask in bad air. Also, foam is flammable until it’s fully dry, which can take 24 hours. So, avoid smoking, turn off pilot lights, and keep areas well-ventilated.
Essential Tools and Materials for Smoothing Foam
Smoothing expanding foam needs specific tools and materials for a perfect finish. As a seasoned DIYer, I’ve found that the right tools make a huge difference. Let’s explore the key tools you’ll need for this task.
A utility knife with an extendable blade is essential for trimming and shaping foam. It lets you make clean cuts and remove any rough edges. Also, a serrated bread knife is great for cutting through big foam sections, even in hard spots.
For bigger foam jobs, a flush-cut foam saw with a flexible blade is a must. These saws cut through thick foam smoothly. If your project is huge, consider renting an electric foam saw for better efficiency.
You’ll also need a metal scraper to smooth out rough surfaces. Plus, sandpaper (80-120 grit) and a sanding block for a flawless finish. Don’t forget the putty knife, wall filler, foam roller, and paint for the final touches.
With this essential toolkit, you’re ready to tackle any foam smoothing project. The right tools are key to success. With this list, you’re on your way to a professional-grade finish.
Proper Safety Equipment and Preparation
Working with expanding foam requires safety first. Make sure you have the right gear before starting. This includes safety goggles, coveralls, and a respirator to protect your eyes, skin, and lungs.
Getting your workspace ready is also important. Open windows or use fans for good air flow. Cover nearby surfaces with tarps or plastic to catch any foam spills. This makes cleaning up easier after you’re done.
Required Personal Protective Equipment
- Safety goggles to protect your eyes from foam particles
- Coveralls to cover your skin and prevent contact with the expanding foam
- Respirator to filter out any fumes or airborne particles during application
Workspace Preparation Guidelines
- Ensure the work area is well-ventilated by opening windows or using fans
- Cover surrounding surfaces with disposable tarps or plastic sheeting to catch any foam pieces
- Remove any clutter or obstructions from the work area for easy movement and access
Ventilation Requirements
Good air flow is key when using expanding foam. The fumes can be harmful if not aired out. Open windows or use fans to keep air moving and avoid harmful vapors.
Safety Consideration | Requirement |
---|---|
Uncured Foam | Wear safety goggles, coveralls, and a respirator |
Cured Foam | Goggles and respirator not necessary, but gloves are recommended |
How to Smooth out Expanding Foam
Smoothing out expanding foam is easy with the right tools and techniques. It doesn’t matter if you’re using open-cell or closed-cell foam. The key is to be careful and methodical. Here’s a step-by-step guide to get a smooth finish.
Begin by holding a utility knife against the wall at the top of the foam. Saw back and forth, keeping the blade flat. For corners, cut one edge, then the other. This makes your cuts clean and straight.
For foam on studs, a metal scraper works well. Gently scrape the foam to smooth it out. Be careful not to damage the studs.
After trimming, sand the foam with 80-120 grit sandpaper. This will make it smooth and even. Always wear safety glasses and a dust mask to protect yourself.
- Trim the foam with a utility knife, keeping the blade flat against the wall.
- Use a metal scraper for rigid foam on studs to achieve a smooth surface.
- Sand the trimmed foam with 80-120 grit sandpaper for a uniform finish.
After sanding, apply wall filler to make the surface flat. Once it dries, paint it to match the walls. This will complete the look.
Technique | Tool | Application |
---|---|---|
Trim foam | Utility knife | Cut through expanding foam with back-and-forth motions, keeping the blade flush against the wall. |
Smooth rigid foam | Metal scraper | Gently scrape the foam on studs to create a smooth surface. |
Sand smoothed foam | 80-120 grit sandpaper | Use sandpaper to achieve a uniform, smooth texture on the trimmed foam. |
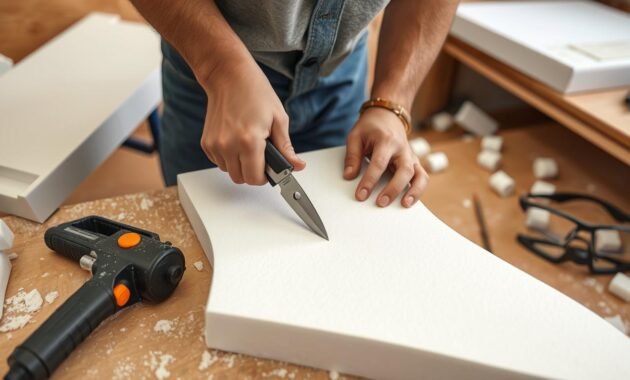
By following these steps, you can trim foam, cut expanding foam, and remove excess foam effectively. With the right tools and techniques, your foam projects will look professional and polished.
Curing Time and Temperature Considerations
When working with expanding foam, curing time and temperature are key. Knowing the best conditions and how moisture affects the foam is vital for success.
Optimal Curing Conditions
The curing time for expanding foam varies by type. Open-cell foam dries in 1-4 hours, while closed-cell foam takes 12-24 hours or more. The best temperature is between 70°F and 80°F. Keeping humidity below 50% helps the foam dry faster.
Moisture Effects on Curing Process
Moisture greatly impacts expanding foam curing. A bit of humidity can speed up the process. But too much can harm the foam’s stickiness and performance. It’s important to check the area’s moisture and adjust as needed, like misting dry spots before applying foam.
Foam Type | Curing Time | Temperature Range | Humidity Level |
---|---|---|---|
Open-Cell Spray Foam | 1-4 hours | 70°F – 80°F | Below 50% |
Closed-Cell Spray Foam | 12-24 hours | 70°F – 80°F | Below 50% |
Understanding curing time, temperature, and moisture effects ensures a smooth foam application. This leads to a durable and effective insulation solution.
Using Cutting Tools Effectively
Getting the right tools and techniques for cutting foam is key. Whether you’re working on small or big areas, knowing how to use different tools is vital. It ensures your work looks professional.
For small foam pieces, a utility knife, serrated bread knife, or foam saw works well. Hold the blade flat against the wall and saw back and forth. This method gives you a clean cut without damaging the area around it.
For bigger foam areas, an electric foam saw is your best choice. Place the blade against the wall studs and keep it flat as you cut down. This keeps your cut even and prevents jagged edges.
Don’t forget to dispose of the foam pieces properly. Just throw them away in the regular trash. This keeps your workspace clean and ready for the next step.
Learning foam cutting techniques is important for a top-notch trim spray foam finish. Knowing the right tools and methods helps you achieve smooth, seamless results.
Professional Techniques for Large Foam Applications
Dealing with big foam projects needs the right tools and skills. For tasks like removing large wall sections or cutting through thick insulation, an electric foam saw is key. It can cut through dense foam easily.
Working with Electric Foam Saws
For big foam insulation jobs, renting an electric foam saw is a good idea. These saws are made for cutting through different types of foam. They help you make clean cuts.
Read also: How to Make Rigid Foam Insulation Noise Reduction?
When using an electric foam saw, pick the right blade for your foam. A serrated blade works best for open-cell foam. Closed-cell foam needs a smoother, carbide-tipped blade.
To use the saw well, hold it flat against the wall studs. Guide it down the wall, cutting between studs. This way, you remove all the extra foam. Place a tarp or sheet under the area to catch debris and make cleanup easier.
Managing Extended Wall Sections
The electric foam saw is great for foam insulation removal and large-scale foam cutting on big walls. Work in sections and keep a steady pace for the best results. With the right plan and tools, you can handle tough large foam applications with ease.
Post-Cutting Surface Treatment Methods
After cutting your expanding foam, it’s time to smooth out the surface. This step is key to getting a flawless finish. We’ll look at ways to make the foam surface smooth and ready for the last touches.
Start by using 80-120 grit sandpaper or a sanding block. Gently sand the foam, being careful not to take off too much. Aim for a smooth texture all over. Take your time, as rushing can cause uneven results.
After sanding, apply wall filler or joint compound for a flat surface. Spread the filler evenly over the foam. Let it dry fully before moving on.
Once the filler is dry, sand the area again for a smooth finish. You might need a second coat of filler if there are any spots left.
Now, paint the area with a color that matches the wall. Start with one coat, then check if you need a second coat for an even look.
By using these steps, you can make your foam surface perfect for your project. Remember, patience and detail are important for a professional finish.
Material | Average Cost |
---|---|
Structural Repair Epoxy (18 blobs per tube) | $100 |
Bondo (1-quart can) | $11 |
Epoxy Gun for Wood Repair | $60-$100 |
Foam Gun for Rot Repair | $40 |
Common Mistakes to Avoid When Smoothing Foam
Smoothing expanding foam can be tricky, even for experts. I’ve seen many mistakes, from timing errors to wrong tool choices. Let’s look at common mistakes to avoid for a perfect finish.
Timing Errors and Solutions
One big mistake is cutting foam too soon. Cutting uncured foam can cause uneven edges and weaken the foam. Wait for the foam to fully cure before cutting or smoothing. Rushing can lead to bad results and frustration.
Tool Selection Mistakes
Choosing the wrong tool for foam can also cause problems. Use a fine-toothed saw for closed-cell foam and a serrated knife for open-cell foam. The right tool ensures clean cuts and a smooth finish.
Working with expanding foam in big gaps can be tricky. Apply foam in thin layers to avoid over-expansion and bumps. This method helps achieve a smooth finish.
Another mistake is trying to clean up wet foam spills. Let the foam harden, then remove it with a scraper or knife. Cleaning wet foam can make a mess.
By avoiding these mistakes and using the right tools, you can get a professional-looking foam finish. Remember, patience and the right tools are essential for success with expanding foam.
Cleanup and Disposal Procedures
Working with expanding foam requires proper cleanup and disposal. This is true for both pre-cured and cured foam. Taking the right steps ensures a safe and clean workspace.
To clean pre-cure foam, use acetone or an acetone-based nail polish remover. These solvents can dissolve the foam, making it easy to remove. But, be careful with acetone as it can harm your skin.
For cured foam, you need a more hands-on approach. Use a scraper or sandpaper to remove excess foam. Then, throw away the foam with your regular trash, following local guidelines.
- Use acetone or acetone-based nail polish remover for pre-cure cleanup
- Scrape or sand cured foam to remove excess material
- Dispose of foam pieces with regular household waste
Remember to clean your foam gun after each use. Use a specialized cleaner to keep the nozzle and components free from clogs. This ensures your tool is ready for the next project.
If you spill foam, wait until it hardens before cleaning. Once it’s hard, you can safely scrape or sand it away, just like cured foam.
Cleanup Method | Foam Condition | Key Steps |
---|---|---|
Solvent-based | Pre-cure | Use acetone or acetone-based nail polish remover |
Mechanical | Cured | Scrape or sand off excess material |
Accidental Spill | Cured | Let foam harden completely before scraping or sanding |
By following these steps, you can keep your workspace clean and safe. This also helps protect the environment from foam residue. With a bit of care, your expanding foam project will be a success.
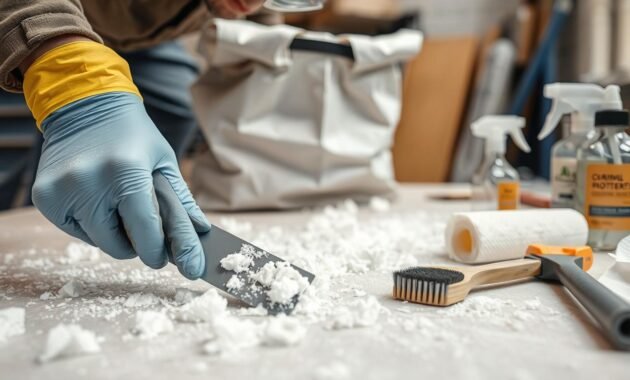
Final Thought
Exploring foam insulation shows it’s great for many home projects. It works well for pole barns or attic insulation. The key is to stay safe and follow the best methods.
Using the right tools and safety gear is important. This way, you get a clean, professional finish. It makes the insulation look good and work better.
Knowing foam insulation tips and best practices is key. Understand the foam’s properties and pick the right type for your job. Also, talk clearly with your installer about what you want.
With the right approach, insulation goes smoothly and efficiently. You’ll get the results you want.
The secret to great foam insulation is in the details. Stay safe and do the job right. This way, you can improve your home’s energy use, comfort, and look.